硫化罐的自动化控制技术近年来取得了显著进展,主要体现在以下几个方面:
1. PLC与DCS控制- PLC控制:可编程逻辑控制器(PLC)广泛应用于硫化罐的自动化控制,具备高可靠性和灵活性,能实现温度、压力、时间等参数的精确控制。
- DCS控制:分布式控制系统(DCS)适用于大规模生产,通过集中监控和分散控制,提升了系统的稳定性和可扩展性。
2. 智能传感器
- 温度传感器:高精度传感器实时监测硫化温度,确保温度均匀性。
- 压力传感器:实时监测罐内压力,防止超压或欠压。
- 其他传感器:如湿度、流量传感器等,进一步提升控制精度。
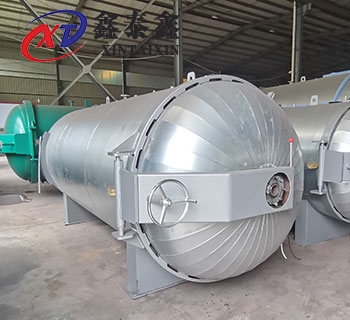
3. 先进控制算法
- PID控制:比例-积分-微分(PID)控制算法用于精确调节温度和压力。
- 模糊控制:模糊控制算法处理复杂的非线性系统,提升控制效果。
- 自适应控制:自适应控制算法根据实时数据动态调整参数,适应不同工况。
4. 人机界面(HMI)- 触摸屏操作:现代硫化罐配备触摸屏,操作简便,实时显示运行状态和参数。
- 远程监控:通过互联网实现远程监控和操作,提升管理效率。
5. 数据采集与分析
- 数据采集系统:实时采集运行数据,便于分析和优化。
- 大数据分析:利用大数据技术分析历史数据,优化工艺参数,提升产品质量。
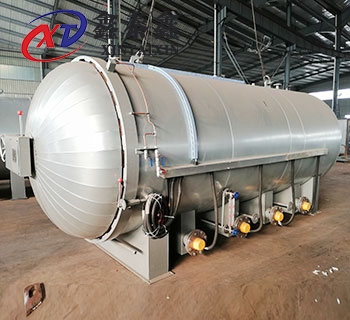
6. 安全保护系统
- 多重安全保护:包括超温、超压、断电等保护措施,确保设备安全运行。
- 故障诊断:自动化系统具备故障诊断功能,及时发现并处理问题。
发展趋势
1. 智能化:随着人工智能和机器学习的发展,硫化罐将实现更高程度的智能化,具备自学习和自优化能力。
2. 网络化:工业互联网的普及将使硫化罐实现设备互联和数据共享,提升生产效率。
3. 绿色化:环保要求推动硫化罐向低能耗、低排放方向发展,节能技术将得到广泛应用。
4. 模块化:模块化设计便于设备的安装、维护和升级,提升灵活性和适应性。
5. 定制化:根据不同行业需求,硫化罐将提供更多定制化解决方案,满足多样化生产需求。
总结
硫化罐的自动化控制技术正朝着智能化、网络化、绿色化、模块化和定制化方向发展,未来将在提升生产效率、产品质量和安全性方面发挥更大作用。